Industry challenge
Our customers expect us to operate without incident. We have plants in the US, Korea, and China where we design and build gas and chemical delivery systems. Our MEGASYS® and field service teams work onsite at our customer fabs. These sites present all the typical hazards associated with ultra-high purity, welding/fabrication, and electromechanical manufacturing. We’re dealing with over 25,000 containers a month.
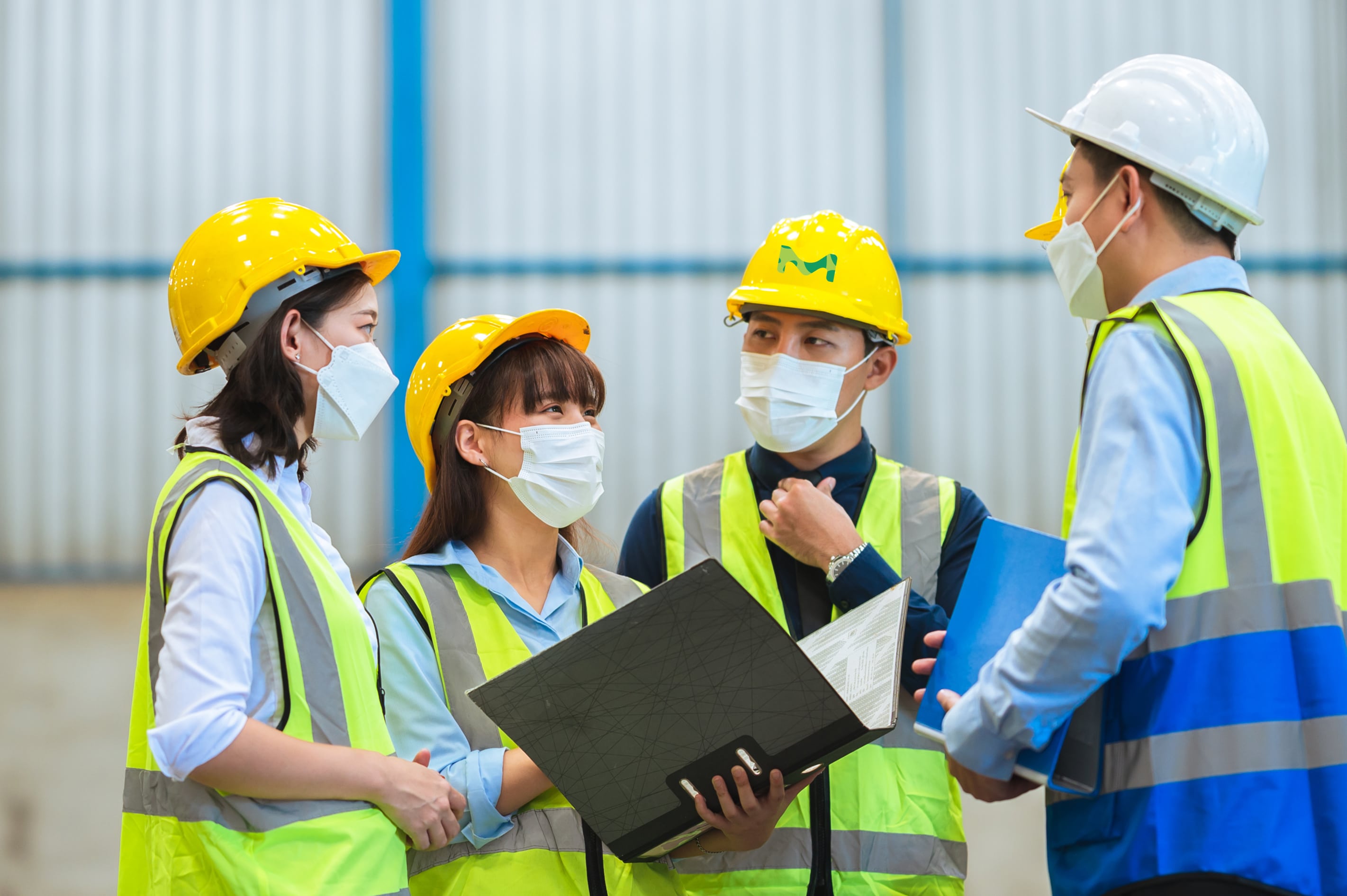
Our Solution: the basic safety process
We believe that all accidents are preventable; we are committed to ensuring that hazards do not harm our team. Given our ambitious safety goal of zero incidents, we utilized combinations of training, coaching, and auditing to support our teams and customers.
The Basic Safety Process (BSP)
Our Basic Safety Process (BSP) involves all levels of the organization, from our newest hire to executive leadership. There are five levels (one for each staff level), and each has its own tracked activities completed regularly. For example:
- Near-miss Reporting Targets
We implemented challenging yet achievable near-miss reporting targets based on site size, scope, and historical safety patterns. All near-misses are tracked and reported each month. Reporting is essential to preventing accidents and we train our employees on the importance of reporting near-misses.
- Root Cause Analysis
To understand the cause of accidents and minimize them, over 35 site managers and leaders attended comprehensive training to help analyze the root causes when investigating incidents and ensure cohesiveness across the organization. They learned how to incorporate this process into their daily decision-making.
- Injury Management Principles
Every employee must return home in the same condition in which they came to work. Employees are required to report any safety or process issues that could impede our safety culture.
- Stop the Job
Our employees are expected to stop the job when something doesn’t feel right; they may not be sure they can complete a task correctly or know the procedure. If any problem becomes evident, the job must stop, regardless of the schedule or customer. Every technician and manager wears a lanyard to remind them of this principle.
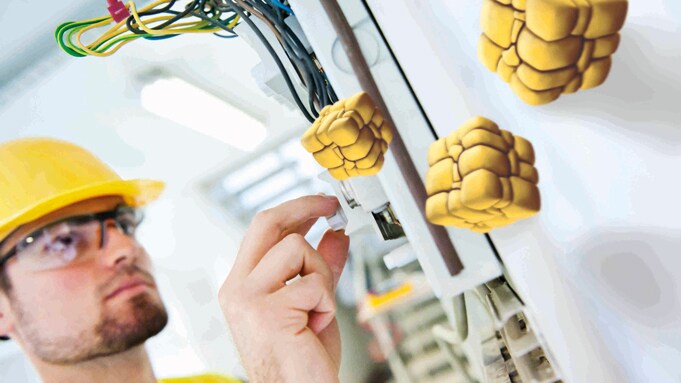
Our breakthrough: a recordable injury rate of zero
The Delivery Systems & Services team closed 2017 with zero recordable injuries in approximately 2 million work hours. During the 2017-2019 period, the entire organization averaged one (1) recordable injury per year. Our average recordable injury rate (OSHA RIR) was <0.1. That is outstanding performance for our industry.
As of November 2021, we have not recorded any injuries for more than 1060 days, and it remains our biggest priority.
Our excellence in safety leads to operational excellence in Quality. Our quality incident metric is at a historical low. Although we do not link the two metrics, it is well-known that safety and operational excellence go hand-in-hand.
Global Impact of operating safely
We believe that our excellence in safety has led to greater operational excellence, renewed contracts and opportunities for growth. The biggest compliment we can receive from customers is when they have observed and admired our safety processes, wanting to adopt them for their own business.
Our goal to keep people engaged and safe has benefited our employees. They come to work with awareness of the hazards and how to mitigate them, keeping them and the business safe.
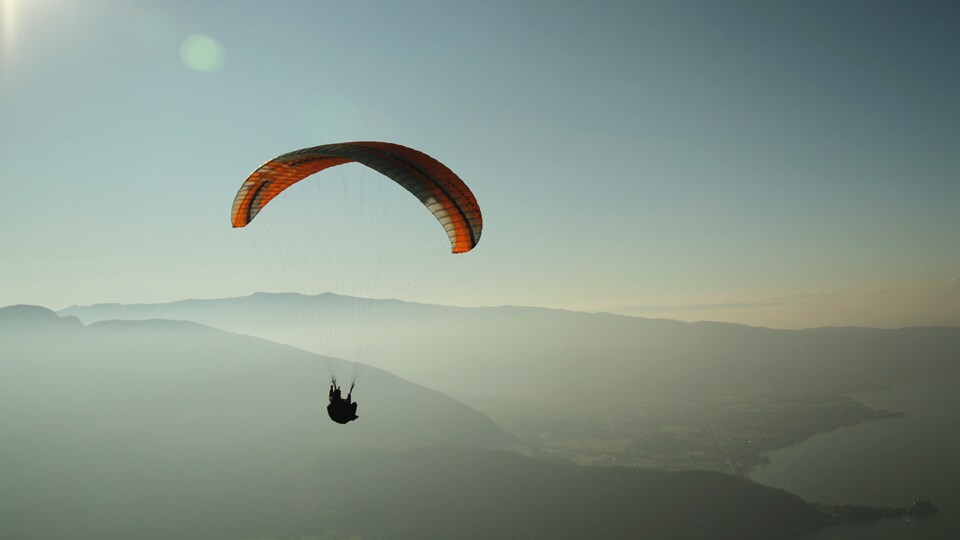