textblock default title
A revolution is sweeping across factory floors around the world. By harnessing advanced technologies such as artificial intelligence (AI), generative AI (GenAI), the Industrial Internet of Things (IIoT), big data analytics, automation, robotics, and other innovations, smart manufacturing – also known as Industry 4.0 – is redefining industrial production.
“Smart manufacturing creates a fully integrated and automated manufacturing environment where machines, systems and processes seamlessly connect and collaborate,” explains Michelangelo Canzoneri, our Global Head of Group Smart Manufacturing. “Its true significance lies in its transformative ability to optimize operations, boost productivity, reduce waste, improve product quality, and enhance human work in operations.”
By leveraging real-time data and predictive data analytics, manufacturers can anticipate and respond to evolving market demands, streamline supply chains and minimize downtime through predictive maintenance. This results in substantial cost savings, improved resource efficiency and a reduced environmental footprint.
“We live in an increasingly volatile world characterized by rising raw material costs, unpredictable demands and supply chain turbulence due to geopolitical events and disruptions such as the pandemic,” says Canzoneri. “Amid these challenges, organizations face delivery delays and uncertainty about when, how and in what format our products are needed. Smart manufacturing capabilities can provide the agility and flexibility to overcome such obstacles swiftly.”
Smart manufacturing represents an industry-wide paradigm shift in how companies design, make and distribute products – from life-saving medicines to cutting-edge electronics. It is set to drive a profound transformation across the industrial landscape, unlocking far-reaching advantages that will reverberate through companies and supply chains, and ultimately benefit people, patients and our planet.
-
2.2
US$ trillion could be added to global GDP through smart factories. [1]
-
3 TWh
could be saved by German specialty chemicals industry annually through smart manufacturing. [2]
-
95%
of manufacturers are using or evaluating smart manufacturing technology. [3]
What is smart manufacturing?
At the heart of smart manufacturing is a vision of highly adaptable, modular “smart factories” capable of rapidly reconfiguring processes, product designs and logistics in response to shifting market dynamics. These intelligent facilities feature reconfigurable production lines composed of adaptive robotic systems, flexible automation cells and self-diagnosing machines that can autonomously optimize energy and resource utilization, predict maintenance needs and seamlessly collaborate with supply networks in real time.
This vision is underpinned by several cutting-edge technological components that work together seamlessly:
- Industrial Internet of Things (IIoT): Networks of interconnected sensors and devices embedded in machinery and products, enabling real-time data exchange and communication between components within the manufacturing environment.
- Artificial intelligence (AI ) and machine learning: Sophisticated AI algorithms and machine learning models analyze vast amounts of data from interconnected systems to identify patterns, make accurate predictions and autonomously optimize processes through intelligent decision-making.
- Generative AI (GenAI): Powered by large language models (LLMs), GenAI enhances manufacturing operations by reviewing and generating documents such as process descriptions, standard operating procedures (SOPs) and electronic batch records. It also assists in creating training materials, optimizing production workflows and providing real-time support and decision-making insights to operators.
- Robotics and automation: Advanced robotic systems and highly automated processes handle complex, repetitive and potentially hazardous tasks with unparalleled precision, efficiency and consistency, enhancing productivity, quality control and worker safety.
- Big data and analytics: Powerful analytical tools process huge datasets aggregated from interconnected IoT devices, machinery and systems to uncover valuable insights, identify bottlenecks and inform strategic decision-making for continuous improvement.
- Digital twins : Virtual replicas of physical assets, production processes and entire systems enable extensive simulations, scenario testing and iterative optimizations in a risk-free digital environment before implementing changes in the real-world manufacturing space.
The convergence of these capabilities translates into a highly optimized manufacturing ecosystem. By integrating automated systems, real-time monitoring and data-driven optimization algorithms, smart manufacturing offers significant potential to reduce downtime, defects, energy consumption, emissions, and waste – at the same time increasing asset utilization and productivity as well as reducing the time to market.
While achieving Industry 4.0 will require significant upfront investment, the potential long-term productivity gains are staggering. According to one industry report, smart factories could ultimately add between US$ 1.5 trillion and US$ 2.2 trillion to global gross domestic product (GDP). [1]
Supercharging productivity with an ecological twist
At its core, smart manufacturing represents a quantum leap in industrial efficiency and productivity, promising a wide range of benefits for both consumers and the environment.
The transition to smart manufacturing will unlock substantial cost savings through maximized efficiency, reduced material waste and optimized resource allocation. Quality assurance can reach new heights through automated inspection and AI monitoring, ensuring stringent standards. Crucially, smart manufacturing prioritizes sustainability by precisely monitoring and minimizing energy, water and material usage – vital for the future of our planet.
The energy-saving potential of smart manufacturing is considerable. For example, a 2022 report revealed that implementing continuous processes, modularization and digitalization in the German specialty chemicals industry could lead to annual energy savings of up to three terawatt hours (TWh). [2] Specifically, if these technologies were adopted throughout Germany, the industry could reduce electricity consumption by 1.3 TWh and heat usage by 1.7 TWh per year – which equates to the annual energy requirements of around 169,700 households, or a medium-sized city.
“Our customers are continuously pushing us to raise the bar, demanding higher-quality products at reduced costs with an accelerated speed to market – all while keeping our service levels high and being more sustainable,” says Canzoneri. “That’s why we’re fully committed to smart manufacturing – adopting this transformative approach will enable us to directly address these evolving customer needs across all our business sectors.”
By integrating real-time data and predictive analytics, manufacturers can anticipate and respond to fluctuating market demands with pinpoint accuracy, dynamically adapting processes, product lines and fulfillment strategies as needs shift. This agility and responsiveness are crucial for ensuring the reliable supply of complex, time-sensitive products, such as vaccines and novel treatments during global health emergencies.
“Anything we can do to strengthen our operations and increase resilience toward any potential challenges or disruptions to the supply chain that may arise, whether that’s another pandemic or a different unforeseen event, is of paramount importance,” says Canzoneri.
Smart manufacturing also enables unparalleled capabilities for the mass customization and personalization of goods. On-demand production of tailored medicines, treatments and consumer products optimized for individual needs and preferences becomes viable at scale. Modular smart factories can cost-effectively produce batches as small as a single customized unit.
“For consumers, all of this translates into better-quality products, personalized to their precise requirements, delivered rapidly and cost-effectively when they want or need them,” envisions Canzoneri.
Our “SMARTfacturing” journey
“This led us to create our overarching smart manufacturing program (SMARTfacturing), identifying how to optimally leverage existing assets, replicate proven successes and strategically invest in company-wide solutions that will accelerate operations and reduce costs across all our global manufacturing processes.”
“As a company with over 350 years of history that has evolved through numerous mergers, acquisitions and expansions, we grapple with a complex patchwork of legacy systems, technologies and processes – presenting a formidable challenge across our global manufacturing operations,” he continues. “We have identified that, in order to fully harness the predictive and prescriptive capabilities of smart manufacturing, we first need to methodically address, streamline and modernize our foundational systems and processes.”
In 2020, we began an extensive initiative to modularize and standardize our production facilities in collaboration with Siemens and Copa Data, with the aim of making our manufacturing processes more flexible and efficient by implementing a software component called the module type package (MTP). This manufacturer-independent standard will enable all the equipment within a production system to communicate seamlessly, transcending the typically fragmented hardware and software currently used in many of our factories.
“To use an analogy, in the past we might have had four basic Lego bricks to build a simple car model – but now we have an incredibly diverse assortment of specialized pieces to construct highly complex, hyper-customized product designs,” describes Sebastian Haertner, our Principal Process Development Project Lead. “From a digital perspective, the MTP can be viewed as the universal connector piece that enables us to assemble all these different components.”
A key benefit of this modular, MTP-enabled approach is that processes can be transferred seamlessly and rapidly from small-scale to commercial production without the extensive manual reconfiguration typically required with traditional manufacturing approaches.
“The MTP provides the vital flexibility of establishing plug-and-produce connectivity between systems and machinery,” says Haertner. “And by creating this seamless underlying integration layer, it is also a key enabler of all of our digital transformation and Industry 4.0 efforts such as advanced data acquisition, optimization and harnessing the power of AI.”
A smarter, more sustainable future
Smart manufacturing represents the future of industrial production – an automated, data-driven revolution poised to enhance customization, quality and efficiency while reducing waste and costs. As this shift toward Industry 4.0 gains momentum, it holds vast potential to reshape the manufacturing landscape, tackle global challenges and profoundly impact our daily lives.
“I’m really passionate about this transformation because it will propel us toward a more sustainable, socially conscious future,” says Haertner. “It’s a long journey, but we’re actively assembling the pieces to bring this vision to life.”
Our contribution
In 2012, the United Nations set out 17 Sustainable Development Goals (SDGs) that meet the urgent environmental, political and economic challenges facing our world. Three years later, these were adopted by all member states. We are committed to contributing toward these ambitious targets through our work. Our work to drive a transformative shift to smart manufacturing fits under Goal 12 – “Ensure sustainable consumption and production patterns”: Target 12.6 – “Encourage companies […] to adopt sustainable practices”.
Learn more about SDGsWork with us
Transformative careers await
Do you believe in the power of technology? By joining our team, you can help develop innovative solutions to address humanity’s greatest challenges.
View All Jobs Join our Talent Zone
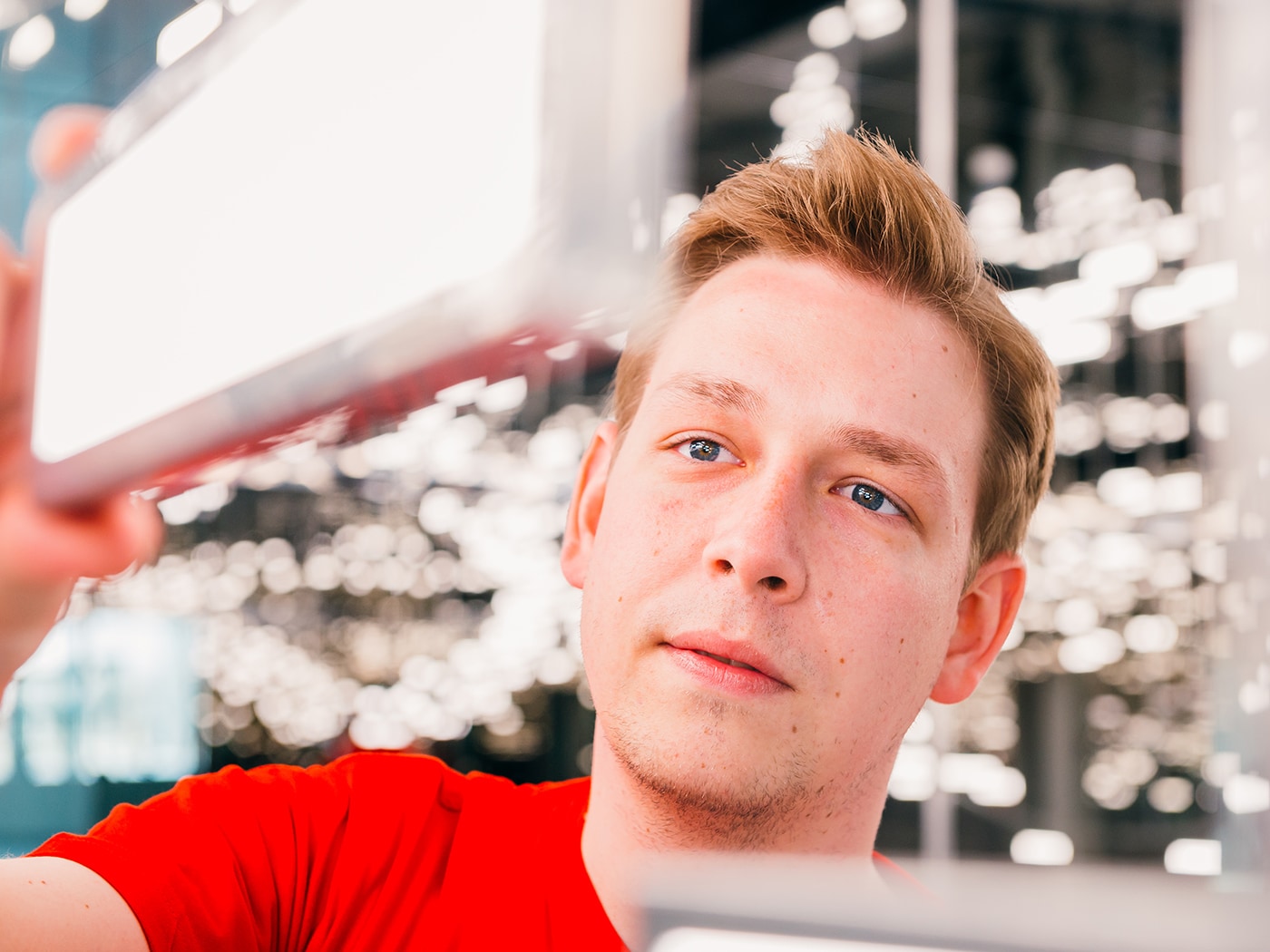