Robots. Making our work safer.
We are integrating robotics across many parts of our business. The goal? To make our work safer and free up the time of our highly skilled workforce, allowing them to focus on creating our next innovations.
From robots to cobots.
Imagine working in an environment where robot colleagues relieve you of menial tasks, goods are delivered to your office by self-driving cars and a robot called Eddy does your supermarket shopping. At our Darmstadt site, this is already reality.
Robots are widely used in many industries to automate manufacturing and production, but as robotics technology advances, we are exploring every possibility.
Since 2018, we have shared a mission of driving digitalization and robotics across all our departments. As part of this collective effort, we have been inviting employees to submit ideas of where and how robotics might be used to improve safety or efficiency. We’ve had more than 100 submissions so far, some of which have led to real-world pilots in collaboration with technology developers and universities.
“Like many companies, we already have well-established robotics technologies in our production lines, to improve the efficiency of handling parts, packaging palletizing products, and in logistics and warehousing,” says Benedikt Ulmke, Project Manager in our Site Management team in Digital Engineering. “But there are also new areas we are evaluating — from using collaborative robots called ‘cobots’ for maintenance and inspection at plants, to the experience of working with humanoids. That is, robots programmed to behave like humans.”
Did you know?
-
3
days is the potential production downtime required for humans to safely inspect a chemical vessel.
-
15
mins is how long a robot takes to get ready to carry out a tank inspection.
-
6
km/hr is the speed of the Starship robot cars.
Making work safer for humans.
One of our pilots involves Spot, a four-legged robot ‘dog’ made by Boston Dynamics that’s being tested for its ability to carry out inspection rounds at a wastewater treatment plant and production facilities in Darmstadt [1] . Seeing through its many cameras and sensors, Spot will find its way around the site, recording and transmitting information, including reading the displays on technical devices. With its powerful zoom lenses, it can also inspect features such as the sliders that regulate the inflow and outflow in the sewage treatment plant pond.
“At the moment, in some plants, a technician has to walk the same route up to two or three times a day to manually inspect the machines. In the future, there might be a robot that can do that,” says Ulmke.
Spot is autonomous and can climb steps, embankments, and walk over grates. But for areas that are harder to reach, such as the interiors of huge cylindrical tanks or reactors in our chemical production plant, we are piloting a different approach — flying drones and robots that can scramble up vertical walls.
Some of these vessels are so vast, scaffolding sometimes needs to be constructed within them before people can carry out inspections. In addition, if a human employee is doing this work, the whole facility needs to be shut down for 1-3 days and all electricity and chemical supplies must be disconnected and safety-checked to ensure that there is no hazardous environment inside before a colleague steps in. By contrast, a climbing robot can be ready to go within 15-20 minutes. They traverse the smooth interior walls using magnets or vacuum suction cups, and relay razor-sharp images of the interior’s condition, allowing personnel to inspect welds and fixtures from outside. This saves employees from the complex and potentially dangerous operation of having to climb into these vessels.
“In addition to relieving the workforce of these unpleasant, challenging inspection tasks and avoiding plant downtime, these robots also bring unique functionality,” says Ulmke. “For example, infrared cameras can find defects in these machines much better than a human being can, generating a digital map of the vessel.”
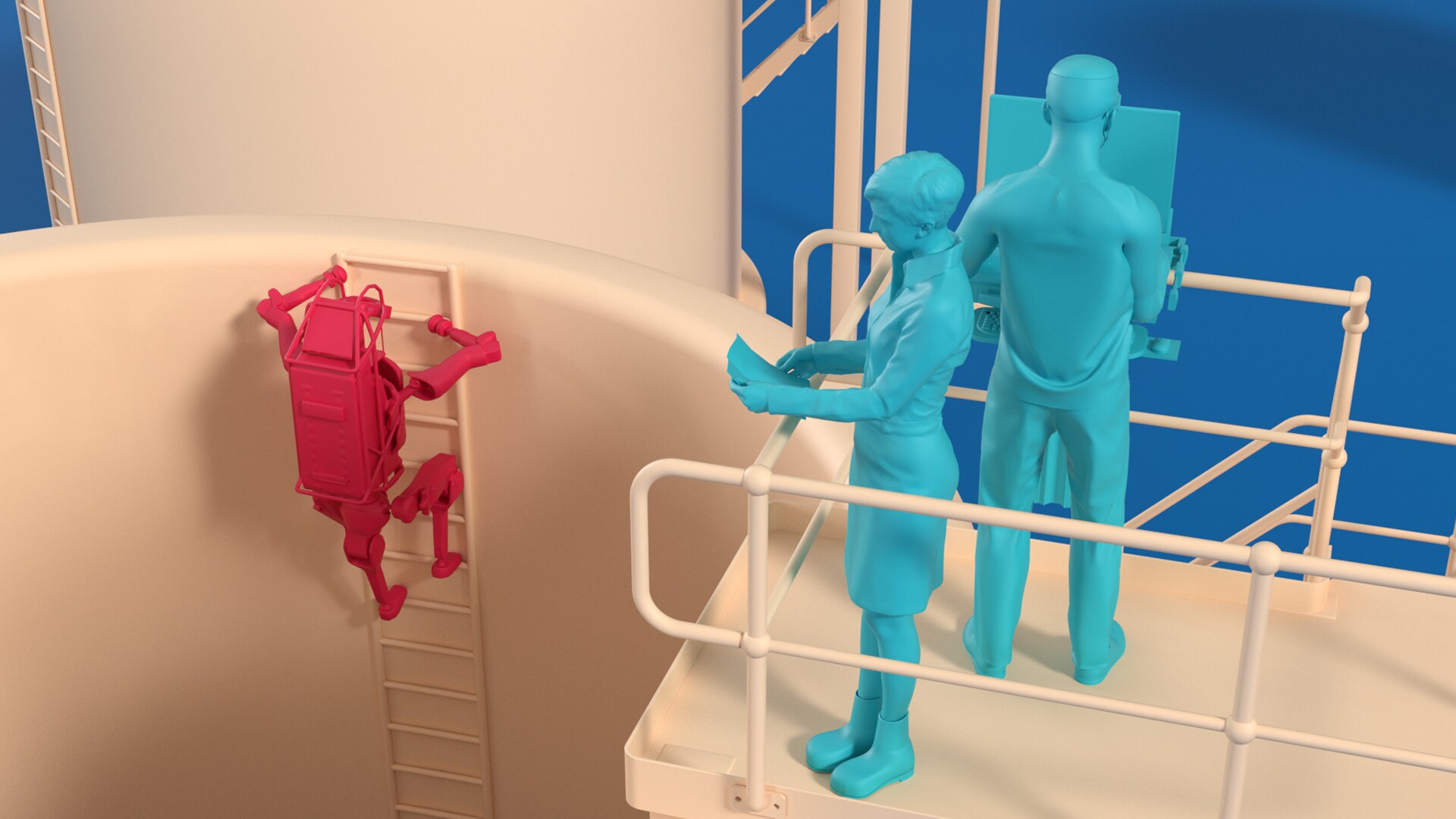
Our helping grippers.
We are looking to robotics to make employees’ work easier and provide them with more freedom to put their expertise to better use. Many aspects of laboratory work involve highly repetitive, manual steps which take up a lot of time for our scientists and technicians.
We’ve already had success in this area in our OLED laboratories. Robots are being used to measure the efficiency of light-emitting diodes, including their luminance, current, voltage, and color spectrum. This time-consuming, complex quality control step was previously the work of technicians. Today, it’s carried out by four cabinet-sized measuring robots. A robot arm, equipped with a microscope and camera, photographs and measures each component, and informs technicians about potential defects.
Similarly, scientists at Darmstadt developed and assembled a custom-made robot as part of our collaboration with the Cell-tech Lab in Poseung, Korea. The robot sorts liquid crystal test cells used in the lab’s research and production process, working through vast trays of jumbled, fragile glass cells, and gently placing each one into a pallet. It uses its camera and gripper arm to pick each one up, moving it to a compressed air nozzle for cleaning, before the final packing step. The robot carries out this task in a fraction of the time taken by a human technician, freeing them up to focus on another research.
Can you buy some milk, robot?
In addition to improving safety and efficiency, robots are enhancing the experience of working at a large site like ours. In 2020, we launched a fleet of autonomous self-driving delivery robots [2]. These Starship robots can carry loads of up to 15 kilograms in a locked cargo compartment and are being used across the site to save time. Employees can summon the robot with their smartphone or computer, load it up with goods and then the robot drives to its destination, where it sends a text or e-mail message to alert the recipient their delivery is ready for collection. “This saves employees time-wasting trips across the site and contributes to increasing efficiency,” says Ulmke.
And more recently, in 2021, we opened our new fully automated supermarket, powered by ‘Eddy,’ open 24 hours a day, 365 days a year. Employees can order their shopping in-store or using an app, and then Eddy – a robot with a gripper arm – packs their purchases at the push of a button, ready for collection.
Industry 4.0 needs robots 4.0
Whereas "older" generations of robots were mainly stationary, today’s robots are mobile and can cruise around. This offers a lot of advantages but also introduces problems for their use in chemical or pharmaceutical production sites. In pharmaceutical production and in our semiconductor business, for example, we have to produce everything according to Good Manufacturing Practice (GMP) standards. But robots are usually constructed for "normal" surroundings, so when they move, their rubber wheels create abrasions that pollute the environment, or they cannot wear such a protection suit. Therefore, decisions need to be made on how far the robot will be allowed to go in these environments.
At our Darmstadt site, we conduct many tests on existing and/or new robots. With these projects, we - as a production site as well as constructors of robots - are learning a lot. For example, what are the requirements for using robots in the chemical industry? Which certifications do you need in the EU? Is the robot declared as a machine or something else?
Learning about these technologies is an important part of our work towards Industry 4.0, which we are collaborating on with Siemens. The aim is to work towards more flexible, modular, and intelligent production processes, and the automation that can be offered by robotics will play a crucial role in achieving this vision.
The tomorrobots.
Realizing new opportunities to use robots to change the way we work can only be done with the help of universities and startups, suppliers, and potential customers. “Wherever we have technologies that are very complex, we rely on a network of partnerships and technology providers,” says Ulmke.
Many of our robotics pilots are being evaluated at our site in Darmstadt — a unique environment for developing these types of technologies. It’s like a city within a city. “It's a good way to test new technologies in a controlled environment,” says Ulmke. “Because the company has three business units and several group functions, we have a very broad portfolio of potential applications for robotic technologies that we can evaluate with our collaborators.”
“We know that technologies like robotics and AI are going to be a reality in our company,” says Ulmke. “We want to find out how we use them to free up time and give employees more scope to use their skills to the fullest, creating new treatments and technologies to improve lives. This is not about replacing employees but to combine the best of both worlds: the accuracy, efficiency and safety of robotics, with the creativity, strategic thinking and personality of humans.”
To accelerate this change, we are partnering with other companies including Bayer, BASF, and Böringer-Ingelheim to build a consortium that calls for the AIRA challenge at the next ACHEMA conference in August 2022.
Our contribution
In 2012, the United Nations set out 17 Sustainable Development Goals (SDGs) that meet the urgent environmental, political and economic challenges facing our world. Three years later, these were adopted by all member states. We are committed that our work will help to achieve these ambitious targets. Robotics fits under ‘Goal 9 — Industries, innovation and infrastructure; Target 9.5 — Enhance scientific research and upgrade the technological capabilities of industrial sectors.’ Integrating robots into our workflows will make our operations faster and more efficient, allowing our workforce to focus on new innovations that empower scientists and prolong and enhance people’s lives.
Learn more about SDGsMeet our robots
-
Delivery drone
Autonomous drone technology offers us the opportunity to save time, money and the environment. Discover how we’ve flown samples on a 25km pre-programmed route.DIVE DEEPER -
Rolling robots
Find out how six-wheeled delivery robots that can navigate autonomously are helping us move goods across our site more efficiently.DIVE DEEPER -
Robots in medicine
Are medical robots with human-like characteristics about to change the way we diagnose medical conditions?DIVE DEEPER -
Spot, our robo dog
Workers at our thermal exhaust treatment plant now have an unusual new co-worker: a highly advanced, four-legged robot. How will it make inspections faster and easier?DIVE DEEPER
Work With Us
Loved robots as a child?
Do you want to work hand in gripper with robot colleagues on new developments? Then join us. We are curious minds in a global company that wants to drive progress in the field of robotics.
View All Jobs Join our Talent Zone
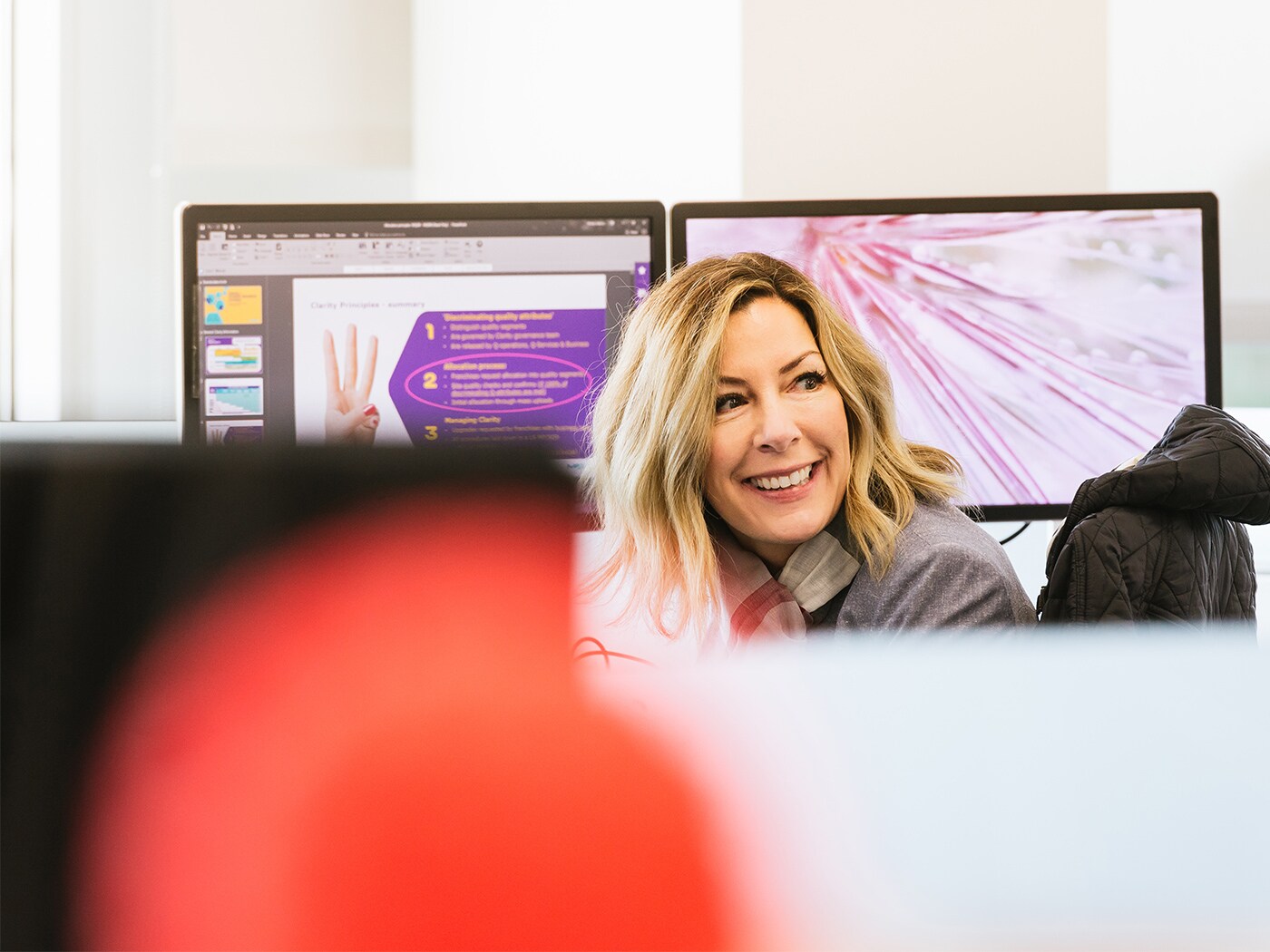