Not too hot, not too cold, but juuuuust right. For biologicals designed to treat conditions ranging from cancer to multiple sclerosis, manufacturing conditions are quite demanding. To ensure nothing spoils the precious batch, pharmaceutical companies usually rely on an intricate multistep process. With a myriad of monitoring requirements and production parameters, it’s less than optimum. Enter Next Generation Bioprocessing: a novel approach with incredible promise for patients and producers alike.
A Delicate Balance
Who doesn’t want to change the world for the better? Most of us feel the need to do something meaningful and worthwhile – it’s simply in our nature. For me that “something” is Next Generation Processing, an exciting new field set to revolutionize the manufacturing of biologics. Isolated from natural sources, biologics – in my case, monoclonal antibodies – have become a vital tool for fighting debilitating diseases like multiple sclerosis, cancer, or rheumatoid arthritis.
The journey of any lifesaving drug is a long and complex one and biologics are no exception. Bioprocessing is a carefully choreographed process to produce biologics that traditionally involves countless validated steps – from filtration and purification to concentration. What’s more, these steps are often repeated several times to keep unwanted by-products in check and ensure that nothing contaminates the batch. Production parameters like temperature, pressure, pH, oxygen content, or flow rate need to be just right. It’s quite a challenge. But thankfully, “meticulous” is my middle name!

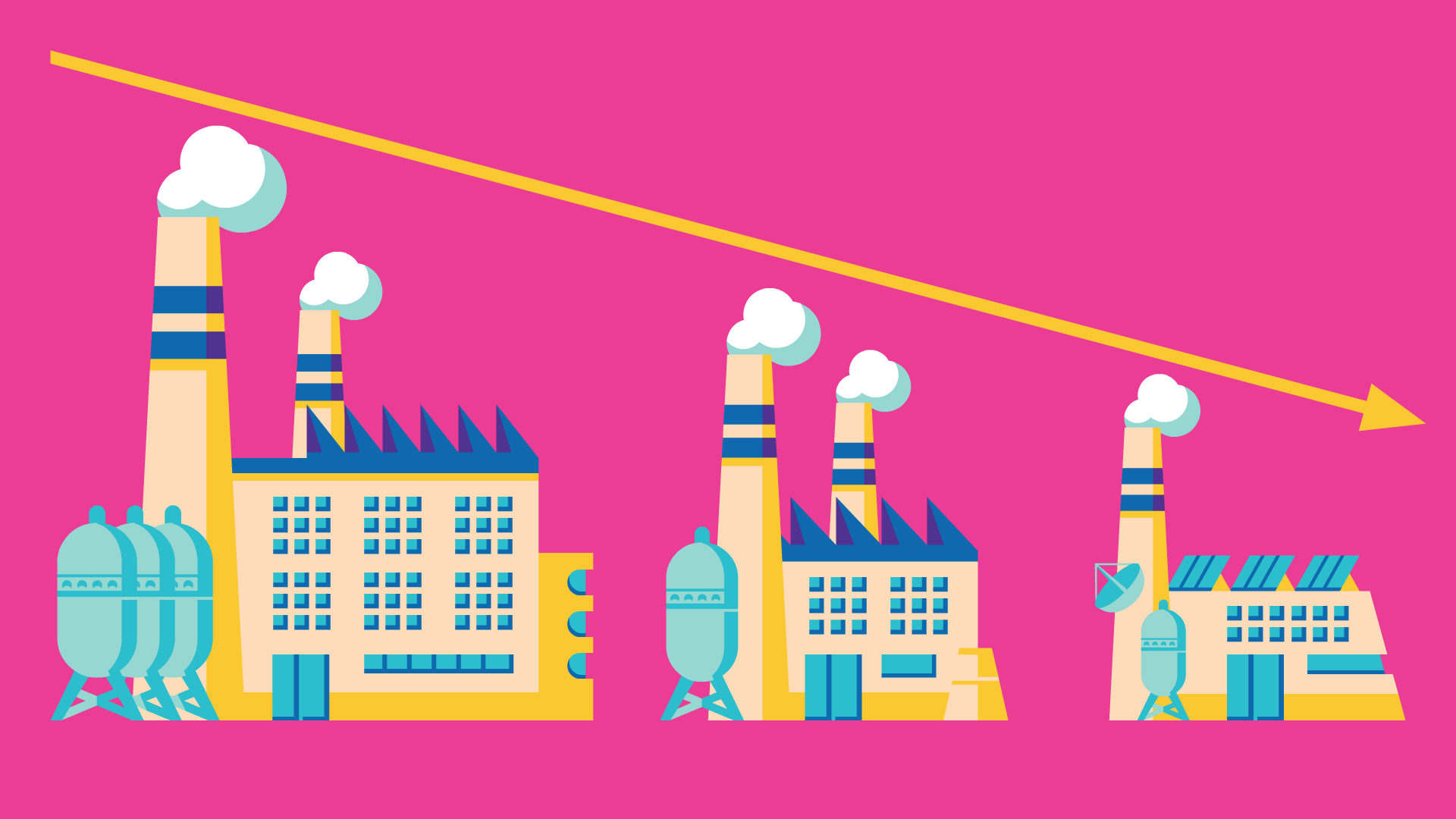
Honey, They've Shrunk the Site!
Everything around us is getting smaller, smarter, and more intuitive, and biopharmaceutical processes are no different. Manufacturers are discovering the benefits of working at a smaller scale. As “Next Generation” suggests, our approach takes bioprocessing to a whole new level. As a process-development scientist, I have firsthand experience of the incredible changes that manufacturing intensification has brought to the industry, to patients – and to my own job.
The most obvious differences are? Size and speed. I don’t want to bore you with technical jargon, but new intensification technologies like perfusion upstream, rapid cycling for capture, or flow-through purification have allowed us to make both equipment and facilities smaller, quicker to build, and a lot less expensive to operate by combining them in just the right way. It’s hard to believe, but by consolidating bioprocessing into a single intensified and ultimately continuous process, we can decrease the footprint of our facilities by up to 80%!
No more huge stainless-steel vats! I won’t miss those. Now, thanks to much higher molecule yields and improved purification, I can run far fewer and smaller batches than before, saving a huge amount of time. Single-use, disposable products reduce the risk of contamination, while integrated, state-of-the-art analytics make it a lot easier to monitor production and spot potential issues the moment they arise. Equipment status and results are just a quick click away. It almost reminds me of the smartphone app I use for controlling the central heating at home!

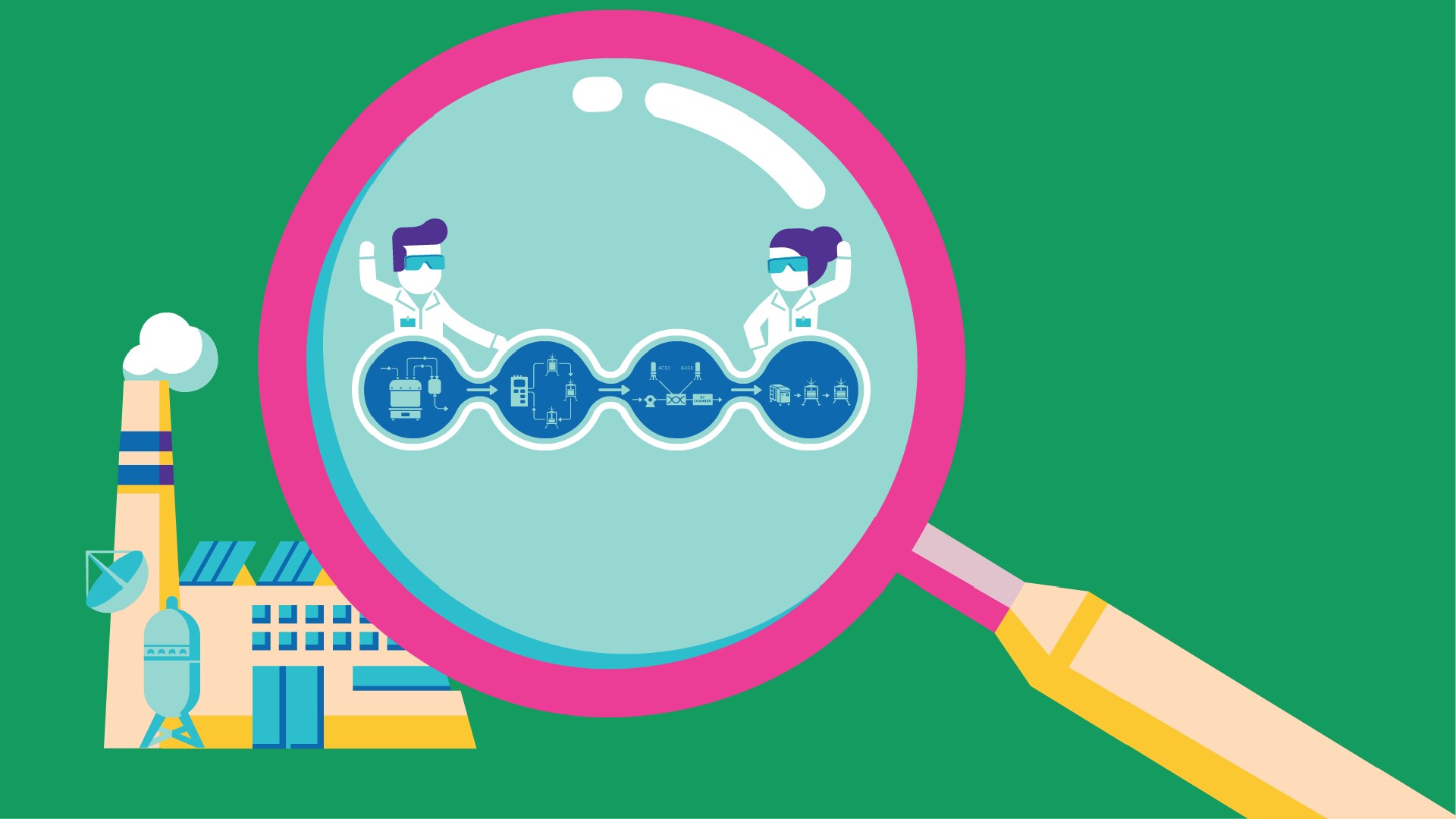
Ramp Up Production, Scale Down Facilities!
To be honest, it’s amazing to be at the forefront of it all. Bioprocessing has been around for decades, but this shift is still very new. I count myself lucky that Merck KGaA, Darmstadt, Germany has been a thought leader in this area since 2012. The company has built dedicated M Lab® Collaboration Centers, where clients can experience the benefits of Next Generation Bioprocessing firsthand. Not unsurprisingly, manufacturers are embracing these new technologies. I mean, what’s not to love about improvements that increase productivity, minimize risk, and improve flexibility? They are rightly excited about the truly staggering savings on time, space, and cost. With their smaller plant footprints and batch sizes, these exceptionally flexible and modular new quick scale-up facilities are especially well suited to emerging countries.
But what’s truly heartening and puts an extra spring in my step is the obvious benefit for patients. Next Generation Bioprocessing accelerates the time-to-market for new drugs, letting people receive treatment faster. Moreover, it does so at a markedly lower cost. Apropos steps: moving from step-based to continuous processing has also cut the number of stages required to get from A to B. With a lot less ground to cover, I can use the time saved to break new ground with state-of-the-art modeling tools to optimize future manufacturing. And, by connecting all the different technologies, I can harness the power of a fully connected and continuous process, helping to make vital treatments more accessible to those who need them, anywhere around the world.
Simplifying processes while maximizing output?