Deposition
Multiple PVD and ALD equipment can be combined for in-situ development and annealing enabling deposition to be carried without vacuum break.
Example: Configuration including two PVD chambers and two ALD chambers and in-situ anneal.
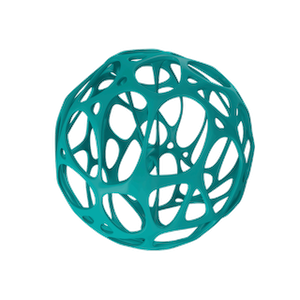
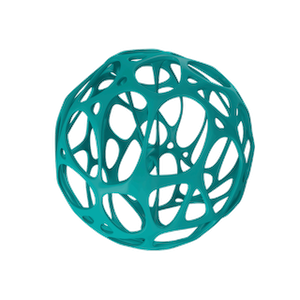
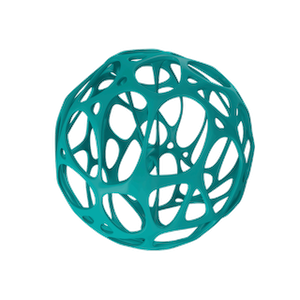
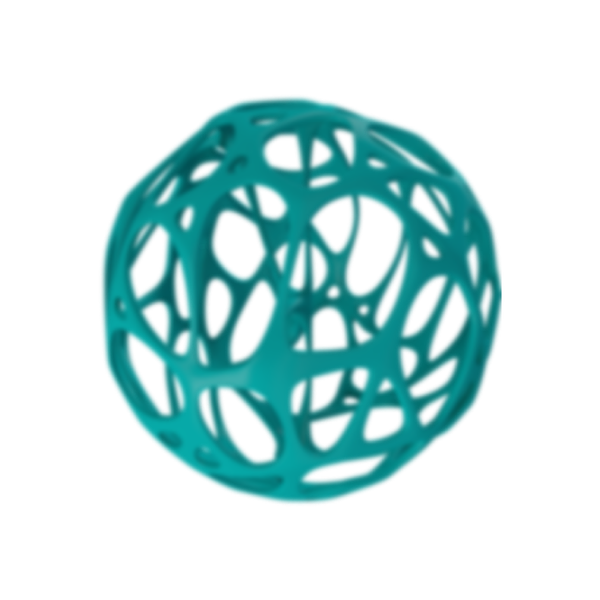
Physical Vapor Deposition (PVD)
Intermolecular®'s physical vapor deposition (PVD) equipment can deposit multiple different materials simultaneously. Performing multiple experiments on a single substrate will accelerate and de-risk materials innovation decisions. PVD deposition allows for rapid synthesizing/screening of new materials across a very large process space (RF and PDC power, pressure, gas compositions, temperature, etc.) and fast exploration of tertiary and quaternary material systems by co-sputtering up to four different targets. The deposition process allows for precise control of doping levels as low as 1% by co-sputtering with power modulation and a wide temperature range for substrate and precise control of temperature.
Types of Physical Vapor Deposition
We utilize two types of deposition depending on the customer’s needs and application.
PVD site-isolated = Deposition of different materials on different dies of a wafer or isolated spots.
- Excellent spot-to-spot accuracy and repeatability Manufacture of MOS and MIM capacitors with in-situ shadow mask, eliminating the need for any clamped masks.
- 2” sputter gun with stationery magnetron and 3” sputter gun with rotating magnetron.
- Developed by Intermolecular for sputtering a wide range of target materials (metals oxides, metal nitrides, chalcogenides and alloys) and large process space.
- Reactive sputtering with oxygen (for metal oxides) and nitrogen (for metal nitrides), and deposition in the presence of forming gas.
- In-situ monitoring of deposition rate with Quartz Crystal Microbalance (QCM).
PVD gradient mode = Intermolecular® can fabricate highly controlled gradient films of up to 10 elements through co-sputtering. Multiple sputter guns are located in a single chamber, with independent control over power, distance, angle, and target composition.
- Gradients of many elements, with location precisely correlated to composition, formed by co-sputtering different elemental materials with guns located at different regions, operating under different conditions.
- Control of the center-point and slope of the gradient along any axis by calibrating the system for each individual target material, and then adjusting deposition parameters for each prior to co-deposition.
- Broad surveys of materials compositions, or focus in on specific regions at high resolution can be performed.
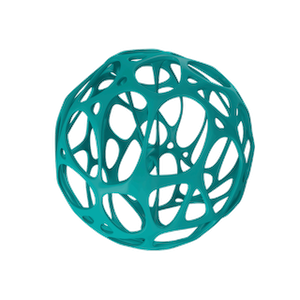
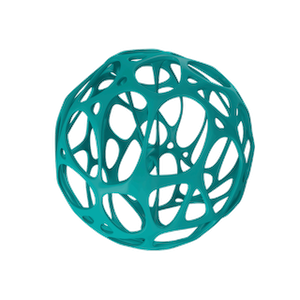
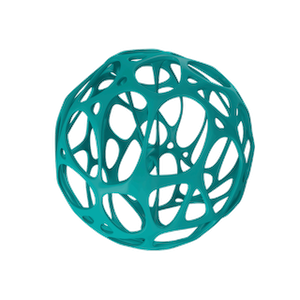
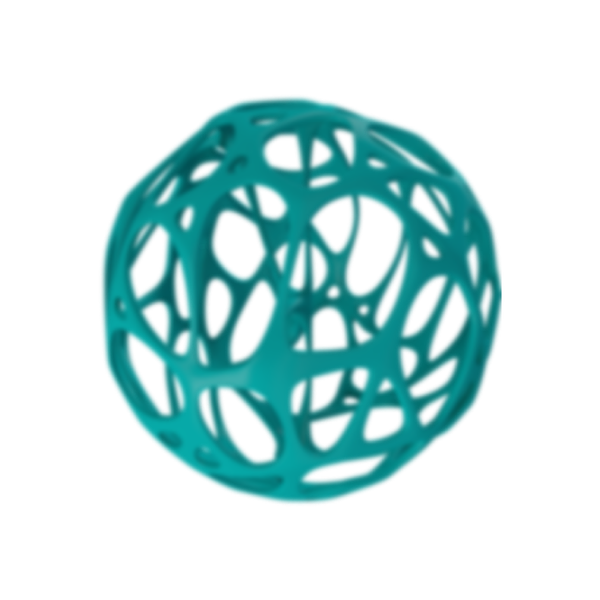
Atomic layer deposition (ALD)
Intermolecular® can deliver results that require materials control at the atomic scale. Atomic Layer Deposition (ALD) is one of the tools used extensively to engineer materials and devices at this elemental level. IMI adds the speed and flexibility of high-throughput processing to ALD with its site-isolated, quad combi ALD reactor technology. Four separate ALD processes can be performed in different regions of the same substrate, simultaneously enabling faster ALD process development and device evaluations.
Chat with an expert
Partnership is the ultimate competitive advantage. Let's work closely together to develop new products and maximize the effectiveness of our R&D.