OLED technology is creating new possibilities
Screens both large and small are now commonplace in our daily lives. From smartphones to TVs to huge public information displays, it’s almost impossible to get through the day without interacting with at least one, if not several.
Until fairly recently, these displays were almost entirely produced using LCD (liquid crystal display) technology, but in the last decade, OLEDs (organic light-emitting diodes) have stolen the spotlight. And they’re now recognized as the gold standard.
OLED technology has opened up a whole array of new possibilities for displays of all sizes. Between thinner, free-form, flexible, printable, wearable, and even transparent displays, the possibilities seem almost limitless. The exciting innovations happening in OLED research are quite literally making the stuff of science fiction a reality.
DID YOU KNOW?
-
40%
of all smartphones sold in 2021 feature an OLED display [1].
-
3x
is the estimated amount by which the OLED display area produced will increase between 2020 and 2027 [3].
-
8m
OLED pixels are needed to create a 4K TV screen [2].
The many benefits of OLED
To understand how OLED technology is driving such developments, we need to take a step back and look at how it actually works.
Each OLED display pixel consists of a stack of thin organic layers sandwiched between an anode and a cathode. Apply a small electrical field, and the OLED starts to emit light. Turn the electric field off and the OLED goes dark, yielding a black pixel. The color emitted by the OLED is defined by the organic materials used and the stack design.
Because the organic material itself is emitting light, OLED displays have no need for a backlight, unlike LCD screens. This means that with OLED, you can achieve true black on a display by simply turning pixels off.
The lack of backlighting means OLED screens are thinner, lighter and consume less power than their LCD counterparts. OLEDs can be applied on rigid glass or flexible substrates like plastic or metal foils, turning virtually every surface into a potential display or light source. What’s more, OLED displays deliver
unparalleled color brilliance and high contrast for a richer viewing experience.
Eight million pixels are needed to create one of today’s ultra-high-definition, 4K TV screens [1]. And every one of those pixels has to function perfectly, as the human eye is extremely sensitive to deviations in color and brightness.
OLED displays are a growing feature of everyday life
OLED is already considered the gold standard for displays, with the technology becoming all but ubiquitous across premium TVs and smartphones. But OLED is also increasingly being used in devices like smart watches, computer monitors and virtual reality (VR) headsets.
Historically, most major smartphone manufacturers would outfit only their flagship devices with OLED displays. But so accessible has the technology become that 40% of all smartphones sold in 2021 carried an OLED panel. And in 2022, this figure is expected to reach 45% [3].
“It’s an exciting and dynamic market,” says Johannes Canisius, our Head of Global Product Development. “Our team has the opportunity to lead the way in developing the most advanced display technology in the world.” [1]
“To know that the material I work on is also in the device that I carry with me all day long, and those that my friends and family use,” he added. “That’s pretty amazing. In a way, a part of my work is with them all the time.”
Improving OLED performance and lifespan
While the popularity of OLED technology has grown rapidly in recent years, there is still much progress to be made. We are developing new and innovative hole transport materials (HTMs), a key enabler of OLED evolution.
HTMs play a fundamental role in every OLED stack, controlling the delicate balance of electrical charge across the pixel. The performance of HTMs is directly
reflected in the performance of the overall display. We are using simulation tools and sophisticated analytics to help us fully understand the processes at play in HTMs, from the atomic, right up to complete device scale.
By improving HTMs, we can increase both the efficiency and lifespan of OLED screens, making the technology more reliable and sustainable. We have already made several materials breakthroughs that are enabling new OLED applications for screens large and small. And advanced HTMs promise to address other challenges that are currently limiting OLED performance.
The manufacturing of OLED displays is another component of the technology where improvements are continually being made. Most OLED displays are produced using the vacuum thermal evaporation method. Organic material is heated to form a gas, and then directed to condense on a display surface as a uniform layer. Much like water vapor condenses on a cold window, though much more precise.
Another solution is to print displays using inkjet technology. While the principles of this are not unlike those of your standard office printer, it places much higher demands on the ‘ink,’ as well as the design and control of the printing head. Our researchers are working on perfecting all aspects of the more versatile inkjet printing process, which can significantly reduce OLED production costs.
Flexibility is the future
It’s estimated that the amount of OLED display area produced is likely to increase three-fold between 2020 and 2027 [2]. But it’s tomorrow’s exciting OLED applications that will determine the true appetite for the technology. Early free-form devices, which are impossible to create using other display technologies, have already begun to emerge.
Contrary to the flat, rectangular shape of standard screens, free-form OLED displays offer bespoke shapes and novel design features with surfaces that can be bent, folded, stretched, or rolled. Today, it’s curved TVs and foldable smartphones, but who knows what experiences free-form OLED could enable in the future.
But producing these unorthodox screens presents new challenges. Compared with your standard flat display, for instance, free-form OLED requires the display module’s thickness to be reduced by around 60%.
We’ve created a range of display materials – our liviFlex™ platform – which are helping manufacturers realize their free-from concepts by improving display hardness, scratch resistance, flexibility, and optical characteristics, such as transparency and color. In other words, creating the optimal profile to turn a promising idea into a consumer product.
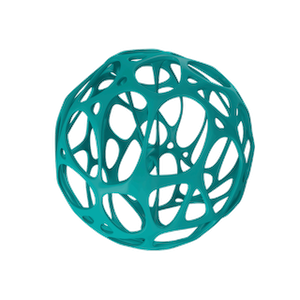
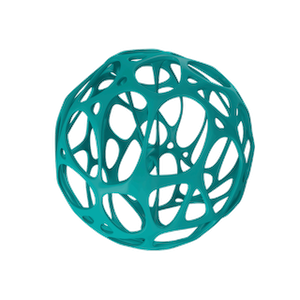
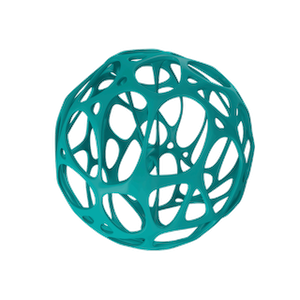
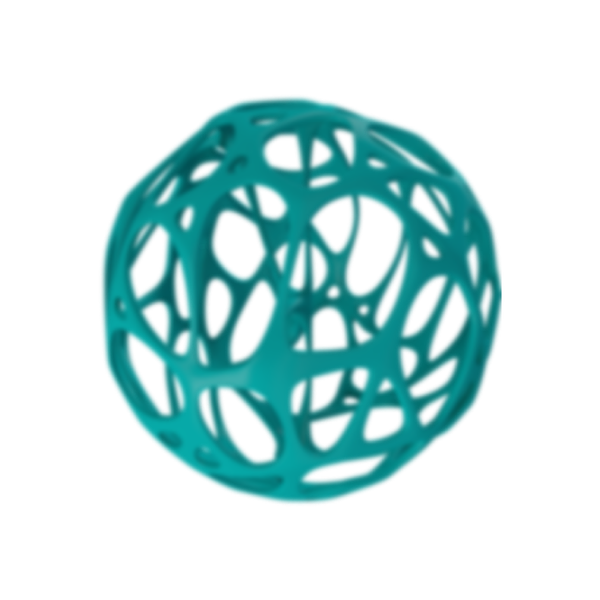
“We’ve been working in OLED technology for over 20 years. Thanks to our established relationships with panel manufacturers and our deep understanding of the display industry, we’re in a great position to push the envelope. The future has never been brighter or more colorful.”
References
[1] https://uk.pcmag.com/features/11619/what-is-4k-ultra-hd
[2] https://www.business-standard.com/article/technology/45-of-all-smartphones-to-be-sold-in-2022-will-have-oled-display-report-121062600248_1.html
[3] DSCC OLED shipment report, published Q2 2021 (www.displaysupplychain.com)
Work With Us
Light up your career.
Do you want to create a future that’s better for everyone? At our company, you can fulfill your personal ambitions and improve the standards of living for billions around the world. Want to learn more?
View All Jobs Join our Talent Zone
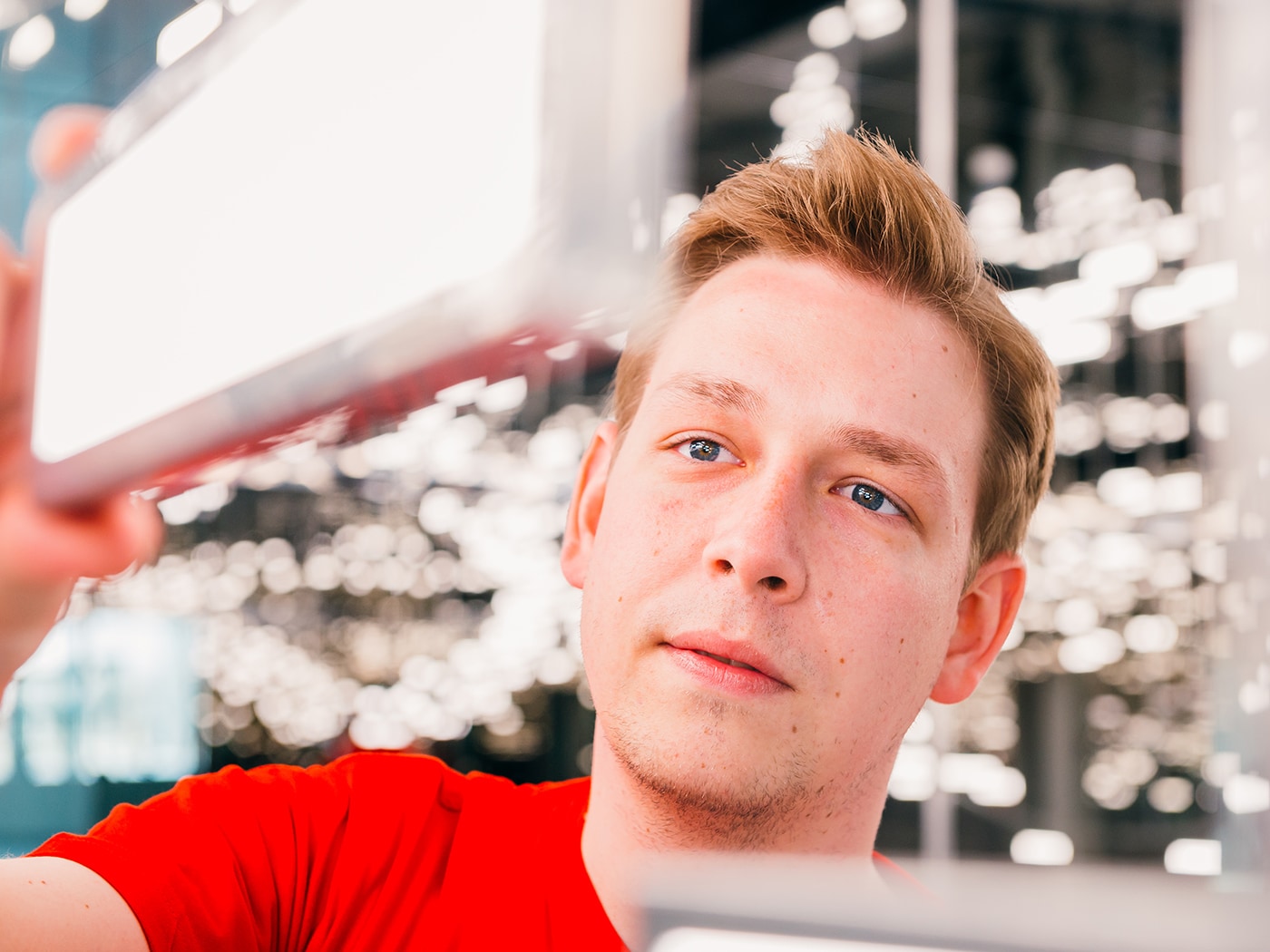