A revolutionary new way of manufacturing components
Computers used to be as big as a room. But now they can fit in your pocket, on your wrist or can even be implanted inside your body. This staggering progress has been enabled by the increasing miniaturization of the components on a microchip, such as transistors – semiconductor devices that act as tiny switches in the circuits at the heart of our computers.
Decades of development, breakthroughs in science and engineering, and billions of dollars of investment have given us vast amounts of computing and huge amounts of memory – leading to the technological megatrends we’re experiencing today, such as AI, the Internet of Things (IoT), and 5G networks.
But the bad news is, we're about to hit a roadblock. The rate of miniaturization of transistors is slowing down, as manufacturers run out of traditional options to create ever-smaller circuitry.
This slow down is happening at the same time as innovation in software relentlessly continues. We are now close to a point where the development of our technology could be limited by our hardware and the prohibitive costs of its manufacture.
Directed Self-Assembly (DSA) offers a revolutionary new way of manufacturing the components that make up computer chips, which could help solve these problems.
Did you know?
-
10nm
and below is the size at which transistor features are now being manufactured.
-
3,000
transistors could fit across the width of a human hair.
-
>40%
of the process steps involved in manufacturing microchips could be cut using Directed Self-Assembly.
Why are new microchip manufacturing processes needed?
To understand why DSA is so important, we first need to understand why current manufacturing processes will struggle to keep up with the continued miniaturization of components.
The transistor used to be a big, bulky device, until the advent of the integrated circuit based on pure crystalline silicon wafers. After 50 years of continuous development, we can now achieve transistor features with dimensions as small as 10 nanometers.
To put this into perspective: a human hair is 100 microns across, a transistor, in comparison is mere fractions of a micron across. You could place more than 3,000 transistors across the width of a human hair.
Besides the obvious benefits of being able to place more transistors on a chip if they are smaller, smaller transistors are also faster and more efficient switches.
So how does the manufacturing process work at the moment and why is it reaching its limits?
Chips are conventionally made via photolithography. In this process, silicon wafers are coated with a light-sensitive material called a photoresist and then exposed to a pattern made by shining light through a filter known as a mask. Wherever light strikes, the photoresist cures; the rest is washed away, and the wafer is then etched chemically to create features in exposed parts of the surface.
For the fastest microchips, which have elements between 10-20 nanometers spaced 80 nanometers apart, this process is repeated about 30 times. Each step requires its own expensive mask, and every step adds time to the process. As we move down towards the scales the industry now wants to achieve – in the 10nm and below range – photolithography will become too expensive and complicated.
"The latest systems for doing this patterning have become so complex that they reportedly cost more than 100 million dollars each," says Karl Skjonnemand, Director, Head of R&D Branchburg, Semiconductor Materials. "And semiconductor factories contain dozens of these machines. So people are seriously questioning: is this approach long-term viable?"
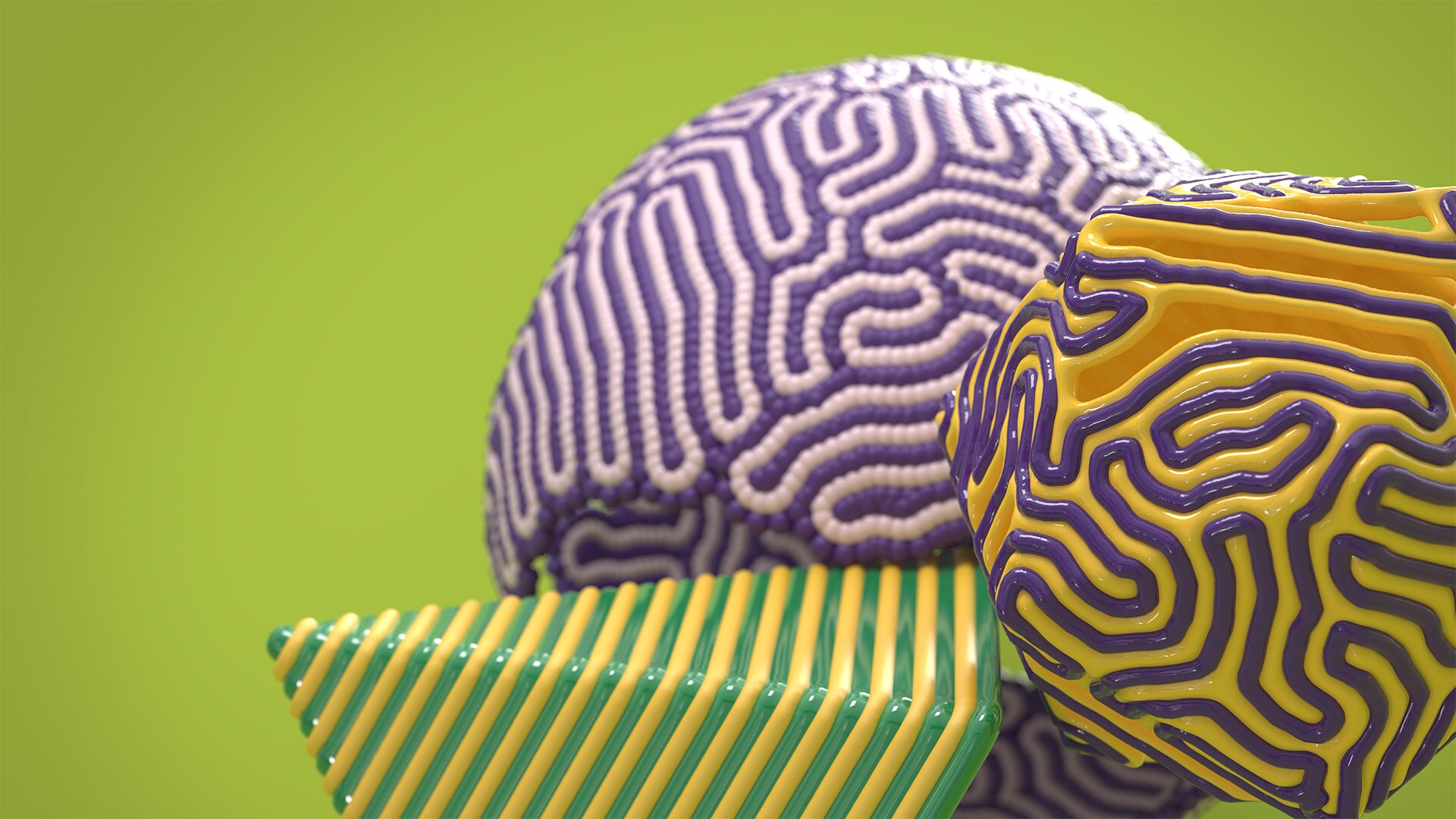
Self-assembly – drawing inspiration from nature to drive new technological feats
We’re working on a totally different and much more cost-effective way of manufacturing computer chips – one that is inspired by nature.
Self-assembly is the process by which an organized structure spontaneously forms from individual components, as a result of specific, local interactions among the components. Self-assembly happens in many different places in biological systems, from lipid membranes to cell structures.
We’re looking at how to take this naturally-occurring molecular self-assembly and apply it to the manufacturing of semiconductor technology.
"If you look at the structure of an integrated circuit, the transistor arrays, many of the features are repeated millions of times," says Skjonnemand.
"It's a highly periodic structure. So we want to take advantage of this periodicity in our alternative manufacturing technique. We want to use self-assembling materials to naturally form the periodic structures that we need for our transistors."
The key to the type of molecular self-assembly we’re developing lies in block copolymers. These materials consist of two polymer chains just a few tens of nanometers in length, which possess special thermodynamic properties that result in highly organized nanostructures.
"These two polymer chains hate each other, they repel each other, very much like oil and water," explains Skjonnemand. "We have billions of these all together in the core material and the similar components try to stick together, and the opposing components try to separate from each other at the same time. So it moves around until a shape is formed."
"And the natural self-assembled shape that is formed is nanoscale, it's regular, it's periodic, and it's long-range, which is exactly what we need for our transistor arrays."
By simply adjusting the volume fraction of the blocks in the polymer chain, it’s possible to yield a number of different regular patterns and shapes. So in other words, we're using molecular engineering to self-assemble nanoscale structures that can be adjusted to the exact pattern, size and periodicity of our design.
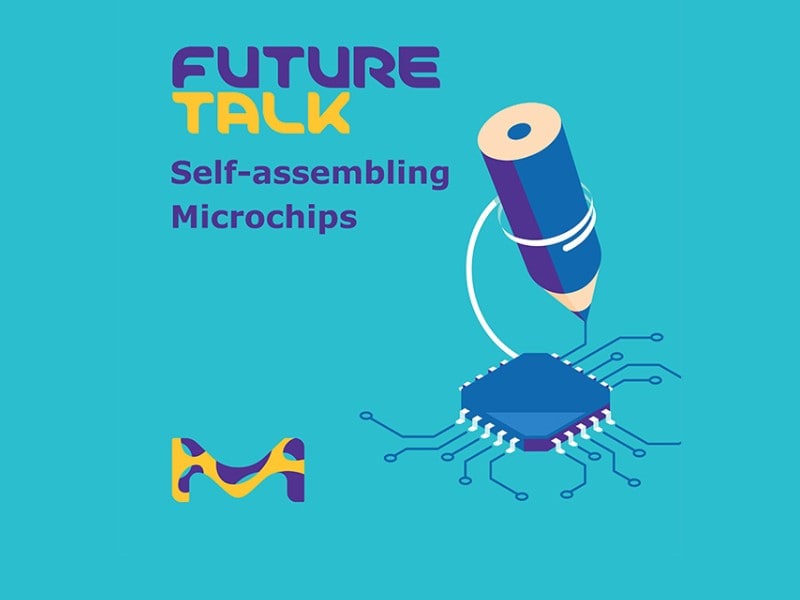
Tune in for our “Future Talk" Podcast
Can you imagine microchips that can assemble themselves at molecular level?! Tune in as our experts explore the many benefits of Directed Self-Assembly technology.
Directed Self-Assembly – a new era of molecular manufacturing
The ability to self-assemble these structures only takes us part of the way towards real manufacturing processes. They still need to be positioned where transistors are required in the integrated circuit.
But we can do this relatively easily using traditional lithography methods to create guide patterns. These carefully direct the block copolymers to create extensive new nanoscale features over the surface of a silicon wafer.
"Let’s take an example," explains Skjonnemand. "If we want to make a fine, 40-nanometer line, which is very difficult to manufacture with conventional projection technology, we can manufacture a 120-nanometer guide structure with normal projection technology, and this structure will align three of the 40-nanometer lines in between. So the materials are doing the most difficult fine patterning. And we call this whole approach ‘Directed Self-Assembly’."
Because traditional lithography is used in DSA, an added advantage is that manufacturers don’t need to make big investments in new equipment. Piloting with our customers has also shown a significant reduction in reported defects during manufacturing compared with conventional multi-patterning.
We estimate that DSA can reduce the number of process steps involved in manufacturing by more than 40%.
A revolution in chip manufacturing is close at hand
So how close are we to DSA becoming part of everyday manufacturing processes?
The biggest challenge, according to Skjonnemand, is that with Directed Self-Assembly the whole system needs to align flawlessly because any tiny defect in the structure could cause a transistor failure. And because there are billions of transistors in a circuit, an almost molecularly perfect system is required.
"We're going to extraordinary measures to achieve this,"he continues. "From the cleanliness of our chemistry to the careful processing of these materials in the semiconductor factory to remove even the smallest nanoscopic defects."
Multiple semiconductor companies are piloting this technology for high volume manufacturing.
"This revolutionary technology is expected to completely change the semiconductor manufacturing process and will accelerate the introduction of next-generation patterning applications," says Anand Nambiar, our Global Head of Semiconductor Solutions.
Our advances in DSA technology are enabling customers to begin planning high volume manufacturing qualifications, which we’ve responded to by developing the exceedingly pure, high volume synthesis capabilities that are key to meeting customer performance and quality targets.
There is growing confidence among our researchers and customers that DSA could, in fact, become an advanced manufacturing process within the semiconductor industry in just the next few years.
And if we can do this, we’ll see ever-smaller transistors produced in a much more cost-effective way, ensuring that the spectacular expansion of computing and the digital revolution continue at pace. It could even be the dawn of a new era of molecular manufacturing.
As Karl Skjonnemand so succinctly puts it: “How cool is that?”
Our contribution
In 2012, the United Nations set out 17 Sustainable Development Goals (SDGs) that meet the urgent environmental, political and economic challenges facing our world. Three years later, these were adopted by all member states. We are committed that our work will help to achieve these ambitious targets. Our work on directed self-assembly (DSA) fits under ‘Goal 9 — Industries, innovation and infrastructure; Target 9.5 — Enhance scientific research.’ Transforming the manufacturing of nanoscale components of computer processors using self-organizing molecules will aid the development of smaller, faster and more efficient microchips that will be necessary to power tomorrow’s technology.
Learn more about SDGs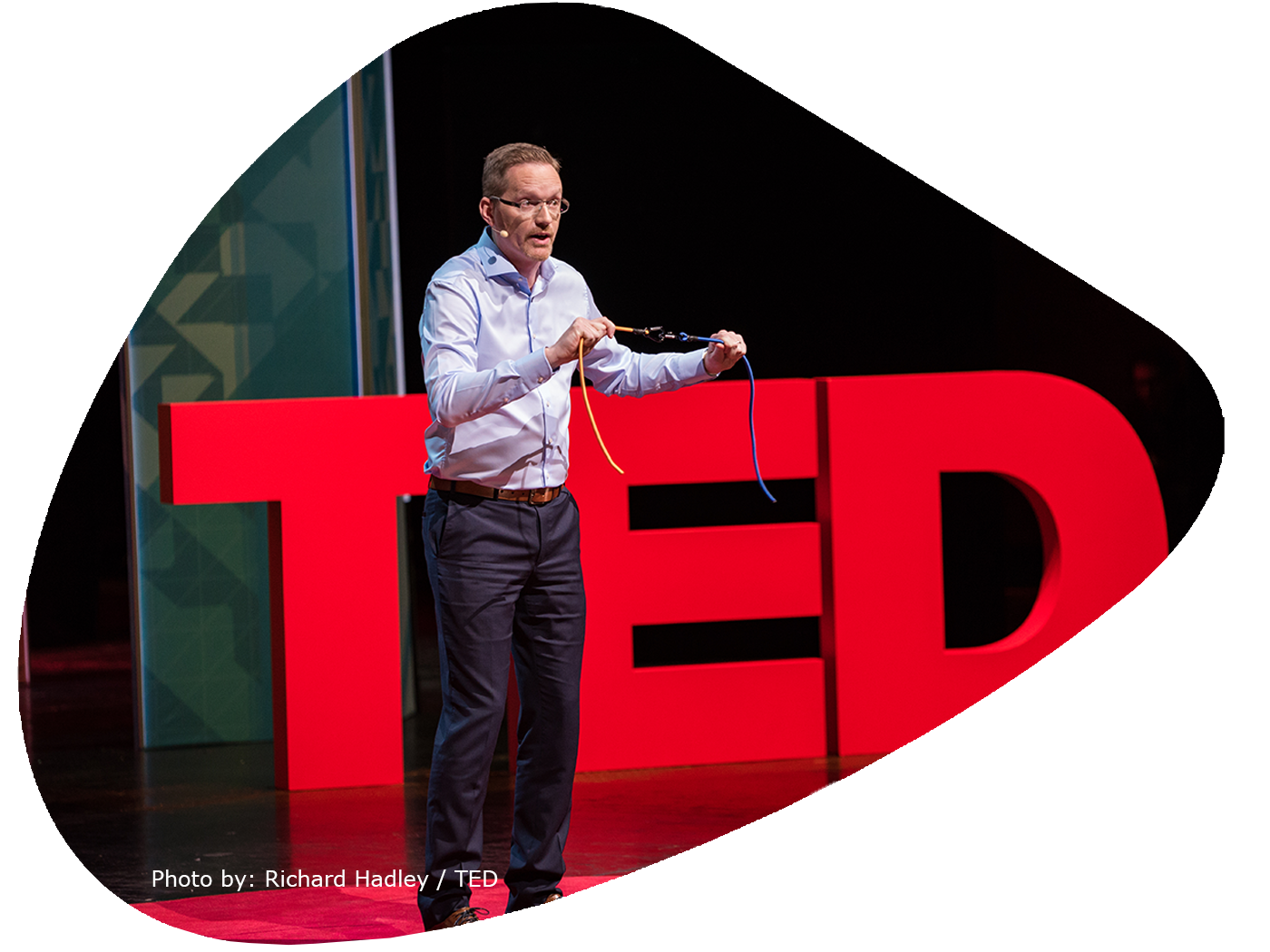
THE SELF-ASSEMBLING COMPUTER CHIPS OF THE FUTURE
Work With Us
Assemble your dream job.
Do you believe that self-assembling molecules are just the beginning? If you enjoy pushing the envelope of what technology can do, work with us to create a smarter, more connected world that will fulfill your personal ambitions.
View All Jobs Join our Talent Zone
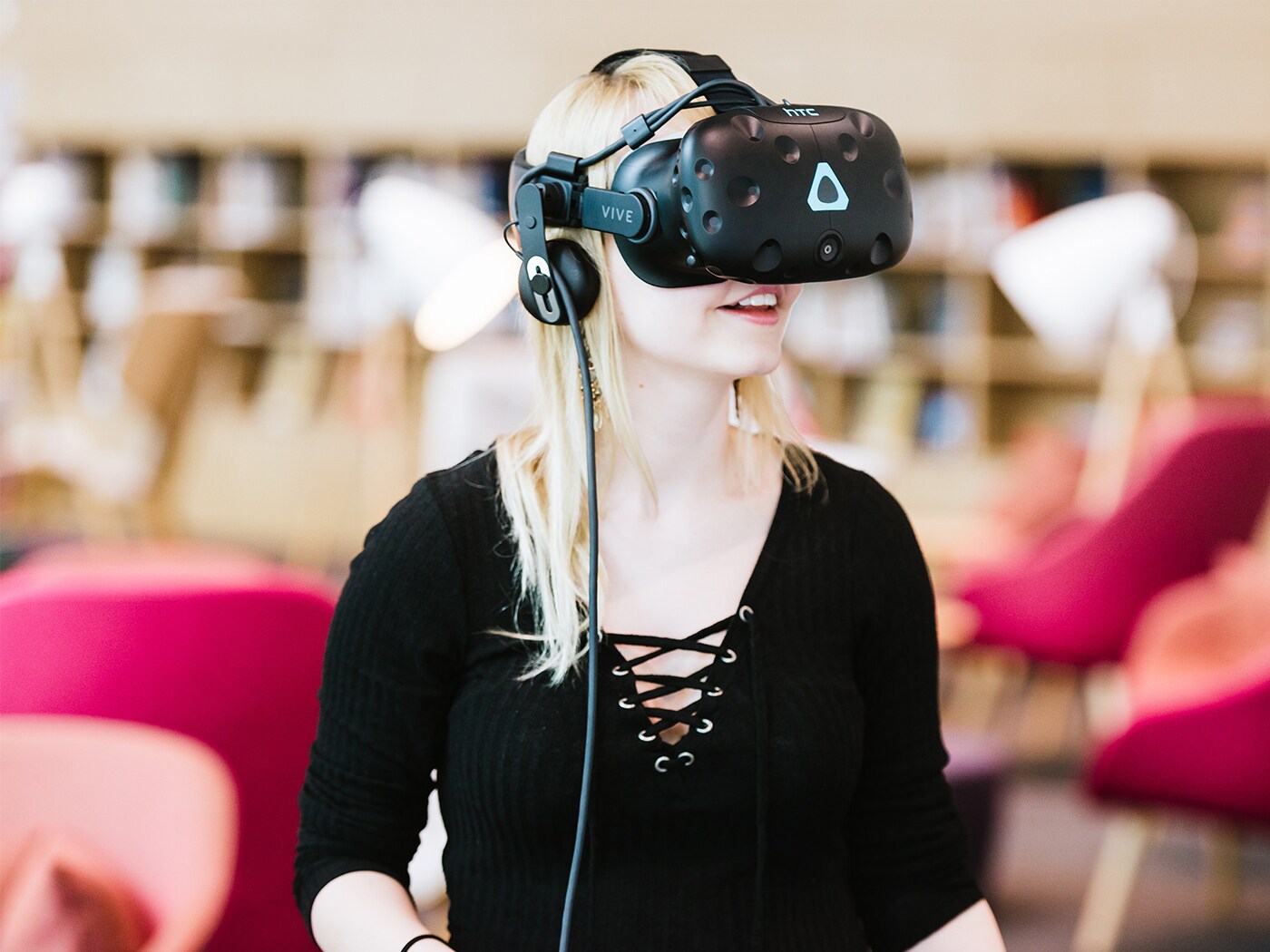